Die Plate For POM
Products: |
POM |
---|---|
Number Of Holes: |
10~30 |
Hole Diameter: |
3~3.6mm |
Diameter: |
120mm~130mm |
Production Output: |
30~ 90 kg/h |
MAAG Pelletizer: |
SPRING-LOADED |
MAAG Pelletizer: | E-SERIES SYSTEM |
Innovating POM Pelletizing Process To Solve Industry Pain Points
POM (polyoxymethylene), due to its unique chemical resistance and excellent mechanical strength, is categorized as a high-end engineering plastic. In the traditional manufacturing industry, metal products are replaced in large quantities.
Pelletizing process, POM melt thermal stability is poor, decomposition at high temperatures to produce formaldehyde gas, corrosive, POM is easy to generate oligomer after cooling attached to the die holes, the rapid accumulation of blocked die holes.
Therefore, POM pelletizing links need to focus on controlling the temperature and speed up the melt flow. For the industry pain points, we create a special POM die plate.
High Precision Machining
Insufficiently smooth inner walls of die holes increase melt resistance and produce pressure fluctuations.
We use EDM equipment and mirror polishing process to ensure the smoothness of the inner wall of the die hole.
Our inspection standards are very demanding: tolerance of hole diameter ±5μm, finish Ra≤0.8μm.
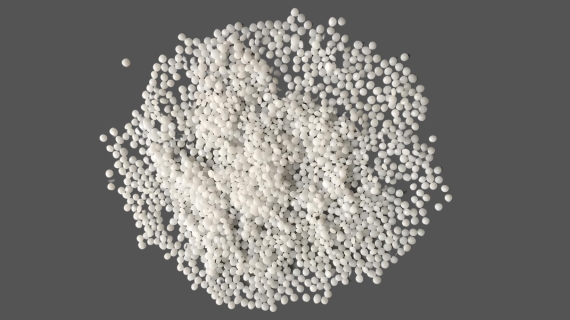
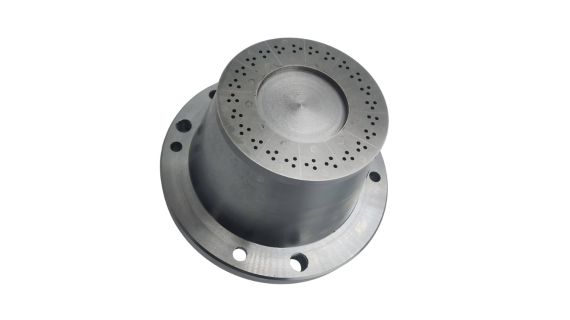
Structural Innovations
Pelletizing belt: honeycomb structure, porous symmetrical type.
Die hole channel: conical flow guide design, shorten the length of die hole.
Heating method: heat-conducting oil.
Combining the above, control the temperature difference ±0.5℃ and improve the extrusion efficiency by 30%.
Tip Material
Formaldehyde is released at high temperatures during POM extrusion. Formaldehyde is corrosive and causes damage to the pelletizing belt and die holes so the pelletizing die plate of POM needs to be a high-strength corrosion-resistant material.
Template material: choose duplex stainless steel and nano nickel-plated coating. Through the ASTM G48 corrosion standard test, formaldehyde corrosion resistance, than stainless steel resistance to enhance 3 times.
Pelletizing belt material: metal-ceramic composite material TiC-NiC or tungsten carbide, hardness up to HRC75.
Template and pelletizing belt, both through diffusion welding, to achieve a seamless combination.
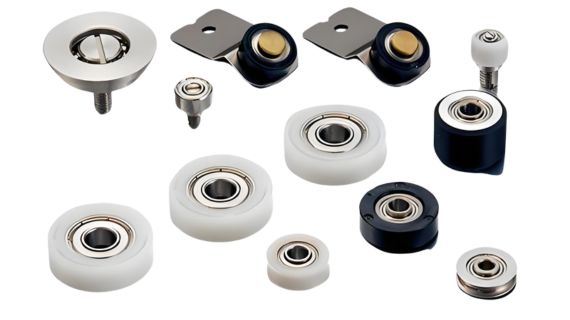
Meeting The Challenges Of The Future
POM plastics are used in conventional manufacturing to meet high precision dimensions and surface finishes. However, in medical and microelectronic applications, the purity of the pellets will be higher, so the underwater pelletizing process will need to be upgraded. We will continue to improve the design and manufacture of POM pelletizing die plate.
Pursuing the goal: precise temperature control, realizing ±0.3℃. Experimenting with new coatings to improve corrosion resistance. Efficient cooling to achieve no sticking.
Give new life to POM pelletizing!