Die Plate For HDPE
Products: |
HDPE |
---|---|
Number Of Holes: |
1496~3104 |
Hole Diameter: |
2.5~2.6mm |
Diameter: |
790~1300mm |
Production Output: |
200,000~ 400,000 tons per year |
CWP Pelletizer: |
ZSK350 ZSK320 |
JSW Pelletizer: |
CMP387 CMP335 CMP308 |
KOBE Pelletizer: |
LCM450G |
DOMIC HDPE Die Plate: High Output - High Wear Resistance - High Precision
One of the keys to underwater pelletizing is the design of the die plate and the coordination of the pelletizing system. Molten HDPE is a highly viscous material, extruded through the die holes, the pelletizing knife rotates rapidly and cuts the pellets, which are circulated to the dryer through the cooling water. The main difficulties of underwater pelletizing of HDPE include the problems of continuous pelleting, tail dragging and end of the material, which can be solved through the design and manufacture of the die plate.
Design Optimization: Decompression Die Plate
The die plate introduces the concept of decompression design. For the optimization of the die hole diameter and the shape of the die hole, the stepped hole design is adopted to reduce the pressure fluctuation of molten HDPE in the extrusion process and improve the uniformity of extrusion.
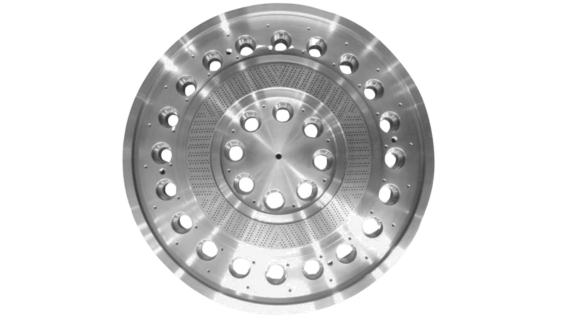
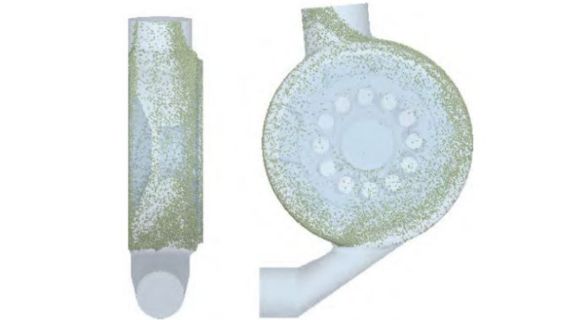
Fluid Dynamics Simulation
Based on finite element analysis and Fluent simulation, simulate the flow of HDPE melt and predict the pressure distribution to ensure the uniformity of die hole extrusion.
Simulate the arrangement density and arrangement of die holes to ensure that the molten HDPE is extruded through the die holes in the best way. Simulation of the thermal channel to ensure that the die holes do not interfere with each other and that the preset temperature stability is achieved.
Simulation of the water circulation system: water flow rate and cutting speed parameters are verified to be integrated to ensure perfect matching of the cutting process, HDPE high viscosity materials, the heat needs to be reduced in time, the molded particles need to be quickly replaced by circulating water, to avoid the production of adhesive particles.
Application Of High Quality Materials
Underwater pelletizer operation state, the die plate is under high temperature and high pressure, the template using tool steel (such as H13 or 1Cr13), with high hardness, high temperature resistance, corrosion resistance, low coefficient of thermal expansion, so that there is a stable material flow channel to ensure the formation of particles.
Pelletizing belt material, using TiC-NiC metal-ceramic composite material, improves wear resistance. Compared with traditional tool steel, the wear resistance rate is increased by 50~60%. After years of verification and customer experience accumulation, TiC content of 30%~40%, the hardness and impact resistance performance is the best.
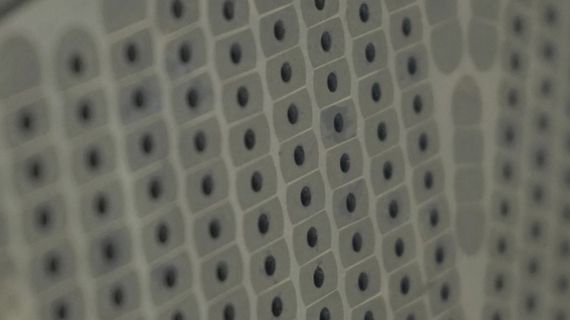
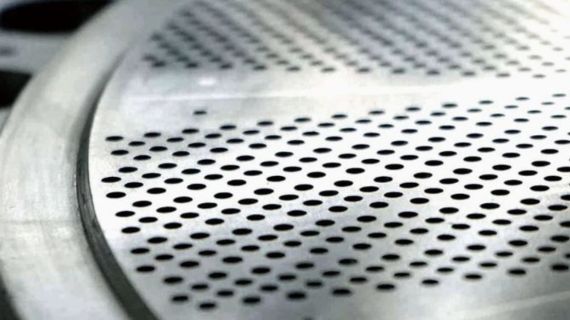
Enhanced Surface Treatment: Coating Process
The use of tungsten carbide coating can improve the use of die plate durability, reduce wear and tear. HDPE belongs to the high viscosity polymer, long time use will produce residue in the runner, and the residue to further produce reaction, hardening and rapid accumulation of heat-conducting material channel blockage, maintenance is difficult.
Case Reference
A large petrochemical company in North America, after using DOMIC die plate to produce HDPE, the life of the pelletizing belt is more than 20,000 hours (the original die plate length of 12,000 hours), and the production capacity has been increased from 800kg/h to 1,000kg/h, with a pass rate of 99.8%.