Die Plate For SAN
Products: |
SAN |
---|---|
Number Of Holes: |
20~160 |
Hole Diameter: |
0.8~2mm |
Diameter: |
280mm |
Production Output: |
80~ 2,000kg/h |
MAAG Pelletizer: |
PEARLO |
Why choose DOMIC SAN pelletizing die plate?
High wear-resistant material: Adopting WC-CoNiCr cemented carbide, the length of time is increased by 1.5 times, which improves the wear-resistance and guarantees the stability of pellets.
Precision design: conical hole flow channel optimization, L/D=6~10, with 1.0~2.5mm hole diameter, to control the expansion of the melt and uniform particles.
SAN Introduction
Medium and large production line with production capacity 1~20t/h for high volume products such as home appliances and automotive with high surface gloss, heat and oil resistance, high rigidity and dimensional stability. Coperion underwater pelletizer is optional.
Small production line, production capacity 200~1000kg/h, for small batch products with special characteristics, such as bottles and medical devices, for products with high transparency and high heat sensitivity. Optional MAAG, Gala underwater pelletizers.
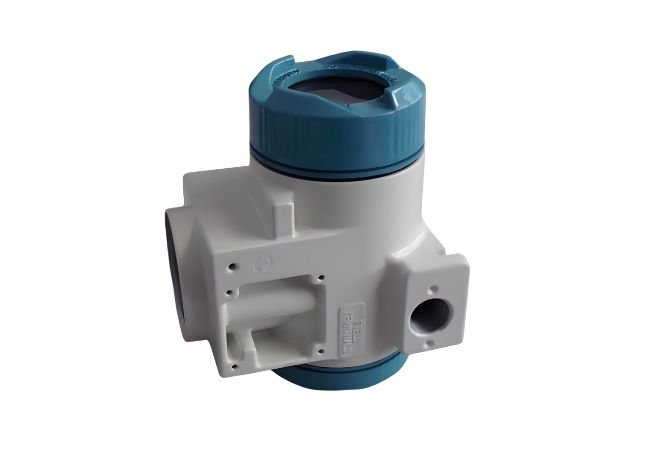

SAN Process
In the process of underwater pelletizing, the molten SAN is extruded through the pelletizing die plate, from the large hole into the small hole, and is cut into pellets by the pelletizing knife at the granulation belt, and then brought to the dryer through the cooling recirculating water, and then into the silo after drying. The die plate is the core of the underwater pelletizer.
Pelletization Requirements
SAN high transparency, high viscosity, avoid thermal decomposition.
Pelletizing die plate need to control the temperature accurately at 200~250°C to avoid heat sensitive acrylonitrile and decomposition at high temperature. The granulation belt of the pelletizing die plate and the inner wall of the die hole need special processing. Ensure high quality of pellets, uniform shape, stable size, smooth surface, no snake skin and trailing phenomenon.


Design Parameters of Pelletizing Die Plate
Basic Parameters: Heating Temperature 230~250℃, Rotating Speed of Pelletizing Knife 800~1200rpm, Outlet Hole of Pelletizing Template 1~2.3mm, Melt Pressure 4~9 MPa.
The length-to-diameter ratio (L/D) setting and the internal smoothness of the aperture are the key factors affecting the uniformity and trailing of the particles.
Optimization of pore shape and flow channel, using conical pore design, L/D=6~10, to control the deformation of the particles when leaving the granulation belt, to reduce the expansion effect. SAN has high melt index, for high melt index should be small pore to reduce the adhesion, usually use 1.0~2.5mm pore size.
Aperture internal smooth, SAN melt flow can be better, to avoid particle surface roughness or clogging. The inner wall roughness of the hole Ra <0.2μm, the conventional use of EDM or laser drilling, and then through the sand polishing process on the inner wall of the hole polishing.
Die Plate Life Cycle
SAN contains acrylonitrile (AN), which is abrasive to the die holes of the pelletizing die plate and the pelletizing belt, and in the long run, it will lead to larger pore sizes and unstable particle shapes and sizes.
Therefore, our pelletizing belt, using WC-CoNiCr is an advanced cemented carbide material based on WC as the hard phase, compared with TiC and traditional WC-Co, reflecting a high degree of one degree, abrasion resistance and resistance to high temperatures, which is an upgrade of the pelletizing belt material.
By examining the appearance of particles and pressure sensing data, comparing and analyzing the aging cycle of the die plate the WC-CoNiCr material is superior to TiC and traditional WC-Co, and the length of use is upgraded by 1.5 times.